
Roller Chains Manufacturers and Suppliers: Maintenance of Roller Chains
What are roller chains?
Roller chains have the advantage of being a relatively simple technique of mechanical energy transmission. Roller chain suppliers offer roller chains made up of several cylindrical rollers joined by links, much like a standard chain-link fence. The chain is moved by a motor-connected sprocket that rotates. The other chain end can then be attached to a portion of the load.
Two bearing locations on a roller chain, a mechanical power transmission component, require lubrication. The chain can flex as it passes around a sprocket thanks to the first bearing point, which is situated between the pin and bushing. The chain links can easily pass over the sprocket teeth in the second location, which is in the gap between the bushing and roller. If you fail to pay attention to the alignment and maintenance of roller chains, then they can get damaged and cause the machine to impossibly fail in its workings.
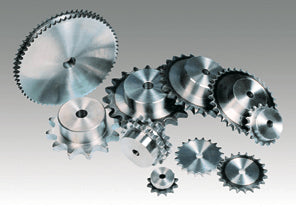
Stick to a maintenance schedule.
Roller chains need regular inspection and service, especially the ones on your conveyors (and their sprockets). Having a maintenance check done on them regularly is a must for proper tension, good lubrication, and alignment. Every three months, chain adjustments and oil and filter changes should be scheduled, while cleaning components, aligning the shafts, relubricating the whole machine, and servicing worn side plates or damaged sprockets should be scheduled for a checkup annually. Projects can be delayed, and heavy machinery can fall or worse, injure others, if the roller chains do not adhere to a strict schedule of checking and maintenance. Below are some tips for the maintenance of roller chains:
Lubrication
Roller chains need to be kept away from dirt and moisture to work smoothly. Most of them need quality, non-detergent, petroleum-based oil. Lubrication reduces wear and offers benefits like heat dissipation. A good lubricant also cushions impact loads, which is why you should avoid using heavy oils and greases, as these are generally too stiff to penetrate the chain's working surfaces. There are 5 different methods of applying lubricant to roller chains that are broken down into types that are usually found in a chain company's catalog or ANSI documentation. It will be based on three main factors: speed, horsepower, and ambient temperature. The different lubrication methods provided by the roller chain suppliers are:
- Manual
- Drip
- Oil Bath
- Oil Disc Slinger
- Pump
The right tension and alignment
The tension of the chain should be regularly checked and maintained to see if it needs adjusting. If the tension exceeds the available adjustment, you need to remove two links and reconnect the chain. If the wear exceeds functional limits or is greater than 3%, then the entire chain will have to be replaced.
New chains should never be connected to a worn chain because they can become rough and damage the drive. If the chain is worn beyond the specified 3%, the operation would not continue as the damage would spread to the roller chain sprockets. Misaligned sprockets are to blame for any perceptible wear on the inside surface of the roller chain's link plates. Hence, regular checks of the sprockets prevent additional sprocket and chain wear.
Conclusion
If you feel that the roller chains have worn out, you can go through the websites of roller chain suppliers provided on the website.
Einen Kommentar hinterlassen