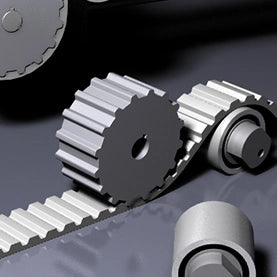
Features and Properties of Polyurethane Synchroflex Timing Belts
Timing belts are built of rubber with strong teeth that can interlock with crankshafts and camshaft cogwheels. These belts are essential constituents of an internal combustion engine that synchronizes the rotating motion of the crankshaft and camshaft.
A continental polyurethane Synchroflex Timing Belt consists of polyurethane and a steel cord tension member of the highest grade. These two components have an excellent bond, which results in a great power transmission capacity. The timing belts are ideal for technical fields requiring synchronous transmission of rotary motion. They are also massively used where switching and conveying tasks are needed.
How Are Polyurethane Synchroflex Timing Belts Made?
High-resistance polyurethane belts are made from waterproof polyurethane and steel cord tension members with high tensile strength. The dimensionally stable and temperature-resistant belts have excellent span rigidity, which decreases very little under extreme load.
These have ambient temperatures ranging from -30 degrees Celsius to +80 degrees Celsius. The Continental brand provides Synchroflex timing belts for particular temperature ranges. Its manufacturing method facilitates an even load distribution during the process of power transmission.
The belts are appropriate for the transmission of high torques and accurate transport of goods.
The Properties of Polyurethane Timing Belts
The highly durable polyurethane Synchroflex timing belts have the following properties:
Mechanical properties
- Low levels of noise
- Resistant to wear
- Zero post-elongation leading to a constant length
- Extremely flexible
- Angular and positional precision
- Ideal power-to-weight ratio
- Up to 80 ms-1 belt speed
- Lower pre-tension
- Concise design
- Resistant to fatigue
- Positive fit
- Ideal for great transmission ratios
- Allows large centre distances
- Lesser bearing load
- Maximum of 98% efficiency
Chemical properties
- Resistant to hydrolysis and ageing
- Resistant from -30 degrees to +80 degrees Celsius
- Resistance to specific acids, alkalines, simple oils, petrol, and fats
Why Is Polyurethane Used in Making Timing Belts?
Polyurethane is abrasive-resistant. It is a highly durable material with long-term reliability, unlike other materials. Polyurethane is immune to substances like oils and grease. These substances are needed by the engine for lubrication.
So, a polyurethane timing belt, despite getting exposed to oil and grease, does not degrade. They also have thermal stability during power and high torque transmission.
The most common materials for fabricating polyurethane timing belts are rubber, PVC, and cellular material. These impart qualities of flexibility, wear, and oil resistance.
Design Parameters for the Selection of Polyurethane AT Timing Belts
The most significant factor in selecting a polyurethane AT series belt is the tooth shear ability. The power capacity is as per the particular shear capacity of every tooth in the mesh relative to the width of the belt.
To select a good AT series belt, consider the following parameters:
- The power that needs to be transmitted.
- The speed of the quickest shaft.
- Drive ratio needed
- The pulley diameters that can be accommodated.
- Driver and the driven equipment.
- Centre distance
- Shaft diameters
Summing up
Polyurethane timing belts are ideal for drives in various types of machinery. These include office machinery, pumps, textile, and printing machinery. The quieter operation, combined with the enhanced positional precision of power transmission, makes these belts best for various uses.
Dejar un comentario